About University of Kashan
University of Kashan was founded at first as an institution of higher education in 1973. It began its activities in October 1974 by 200 students of mathematics and physics. In 1989 more academic fields were added and the institution continued its activities as Kashan Teacher-Training University under the supervision of the Ministry of Science. In 1994, by offering engineering disciplines, this university was acknowledged as the main university by the Ministry of Science. In 1995 College of Architecture and Arts was added to the university with an emphasis on the local needs, art, and industries of the region. Faculty of Chemistry, as the 5th college after Science, Humanities, Engineering, Architecture and Arts, was founded in 2008.
Currently, University of Kashan, within the boundary of 530 hectares and with 80000 square meters of infrastructure (building), in addition to educational campuses, sports facilities, dormitory complexes, restaurant complex, amphitheaters, green spaces, mosque, study halls and health-care center provides leisure, services and comforts to the students. Besides the five mentioned colleges, there are three active research institutes including Nano Technology, Natural Essential Oils, and Energy and also three Research Centers including Kashan studies, Carpet, and Astronomy that contribute to the fact that University of Kashan in recent years has been among the top ten universities in Iran. Accommodating more than 7500 students in 50 disciplines of undergraduate, graduate and postgraduate levels and having about 300 full-time energetic faculty members, this University is approaching the clear future horizons.
According to QS website.
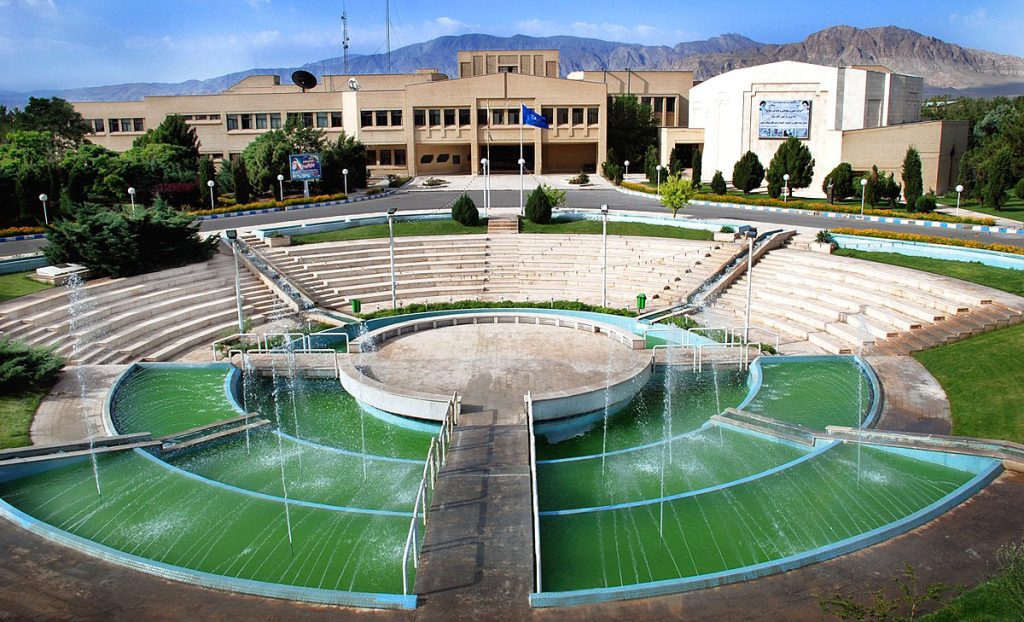
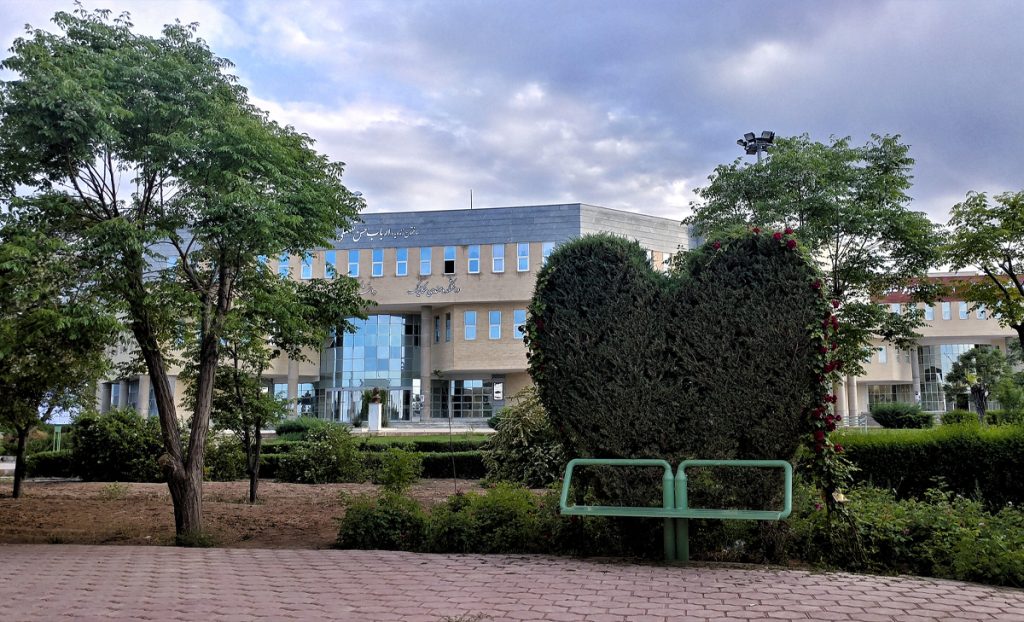
B.Sc. in Chemical Engineering
Location: University of Kashan, Kashan, IRAN
Thesis topic: Simulation of the Lurgi Methanol Production Process and Optimization of Energy Consumption by Aspen HYSYS and Aspen Pinch Software.
GPA: 14.82/20
Supervisor: Prof. Majid Hayati Ashtiani
Sep 2012 – Sep 2016
Dissertation Abstract
Methanol is an important chemical, used as both an alternative fuel and a significant feedstock for the production of other compounds. In this study, the methanol production process at a national petrochemical plant was simulated using Aspen Plus software. The heat exchanger network design, heat targeting charts, and calculation of the energy consumption per unit were carried out using Aspen Pinch software. Moreover, methods for reducing design costs and optimizing energy recovery have been explored. The simulation achieved a 99.99% methanol purity, with an error margin of approximately 0.3% compared to industrial data. Sensitivity analysis determined that a pressure of 76 bar in the syngas compressor (C1) provides the optimal conditions for methanol production and the efficient output waste flow rate should be set at 5%. Different numerical methods, including Broyden, Wegstein, and Direct, were evaluated for simulation convergence and the Broyden method achieved convergence with the highest accuracy and no errors. To minimize practical expenses, the heat transfer area of the exchangers was kept to a minimum. However, this approach resulted in increased costs due to the need for additional auxiliary services. In the adjustment of the heat exchanger network, minimum temperature differences (ΔTmin) of 5, 10, 11, 20, and 30°C were considered. These adjustments took into account the amount of energy crossing the pinch, the costs associated with auxiliary services, the number of converters required, and the overall energy balance. Additionally, temperatures of 155°C, 211°C, and 250°C were analyzed for energy recycling within the system. Finally, a temperature of 10°C was selected as the optimal choice, offering the lowest energy passing through the pinch (32.5722 MW) and the highest economic efficiency, resulting in annual savings of $1,161,555.94. Considering practical and economic factors, 41.4 MW of steam at 5.5 bar and 155°C has been recycled.
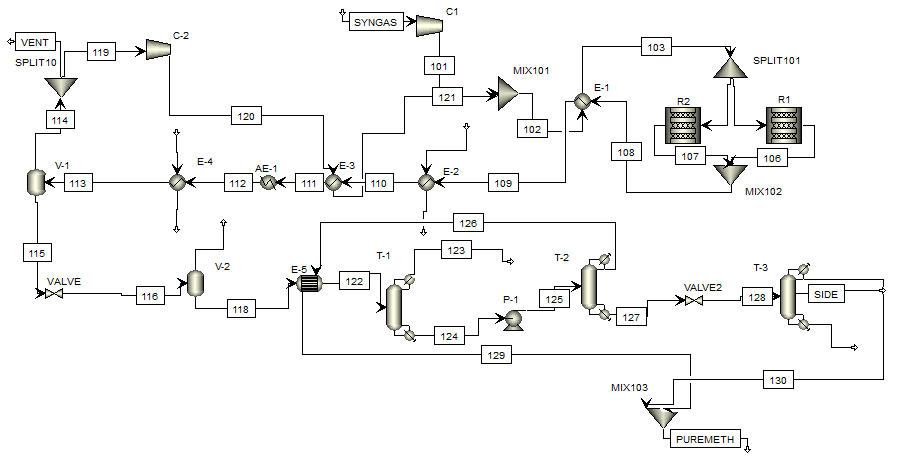
Flow simulation diagram of methanol production and purification process
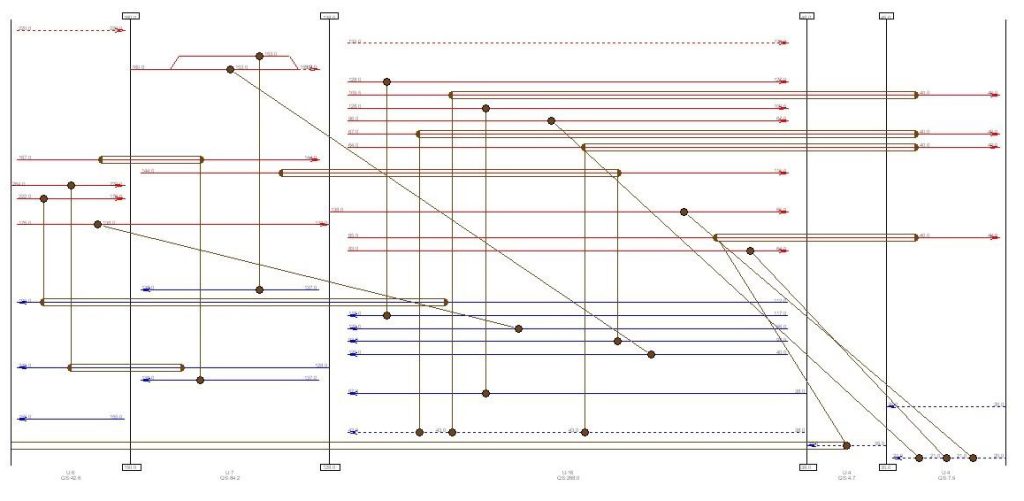
Heat exchangers network after placing utilities
Bachelor's graduation album
M.Sc. in Chemical Engineering - Process Design
Location: University of Kashan, Kashan, IRAN
Thesis topic: Process Design for Barite Ore Solubility Optimization in Oleum and Sulfuric acid via Experimental Design (Response Surface Methodology) and Optimizing the Crystallization of High-purity Barium Salts (BaCl2, and Ba(NO3)2) by Dissolution of Witherite Ore in Hydrochloric and Nitric acids.
GPA: 15.29/20
Supervisor: Prof. Mohammadreza Mozdianfard
Advisor: Prof. Fatemeh Sadat Hoseinian
Sep 2016 – Feb 2020
Dissertation Abstract
Barium salts are widely used in various industries and medical sciences, and despite the presence of abundant mines of natural Barite (BaSO4) in Iran, which is the most suitable source of barium elements for the production of barium salts, they are mainly imported into the country. The extraction of barium ions from barite is done by two processes: reduction and dissolution. In Iran, only the reduction process is used, which, compared to the dissolution process, has the disadvantages of high investment costs, high environmental pollution, and low efficiency. Considering the technical limitations and barite’s insolubility, this research investigated the solubility process of barite. In the first stage, the impact of the effective factors on the solubility process of barite in sulfuric acid and for the first time in oleum was investigated experimentally, and then the optimization of the process was carried out using experiment design software. Parameters of solution temperature (140°C, 160°C, and 180°C), barite particle size (50-100 mesh, 100-150 mesh, and 150-200 mesh), and acid concentration (70%, 80%, and 90% by volume compared to water) as independent parameters and the percentage of dissolved barite was considered as the answer. After performing the specified tests by the experiment design software, the obtained results were optimized and the best conditions and also the most effective parameter for the solubility of barite were obtained.
In the second step, barium chloride and barium nitrate solutions were prepared by dissolving Witherite ore (BaCO3) in hydrochloric and nitric acids. Then, barium chloride and barium nitrate salts were produced by the crystallization process. The important point in the industrial production of these two salts is the concentration of the produced salts in the solution during the crystallization process, which was optimized experimentally using hydro and pycnometers. The results illuminated the optimal density of barium chloride and barium nitrate solutions for achieving maximum crystallization at ambient temperatures, as well as the percentage of the solution that underwent crystallization. Furthermore, XRF analysis revealed a purity percentage of 99.28% for barium nitrate salt and 99.17% for barium chloride salt. FT-IR analysis, in conjunction with a comparison of the absorption spectra of the produced salts with pure samples, confirmed a high degree of conformity and accuracy between the absorption bands, validating the quality of the synthesized salts.
My Thesis Paper
Barite solubility optimization in oleum and sulfuric acid using response surface methodology (RSM)
Mohammad Taghi Rayatia, Mohammadreza Mozdianfarda, Fatemeh Sadat Hoseinianb
aChem. Eng. Dept., University of Kashan, Kashan, IRAN, 8731753153.
bMin. & Metal. Eng. Dept., Amirkabir University of Technology, Tehran, IRAN, 1591634311.
Keywords: Barite solubility, oleum, sulfuric acid, RSM, optimization, hydrometallurgy
Abstract
Barium ions can be extracted from barite either by reduction or acid dissolution in concentrated Sulfuric acid. Industrial application of the former in developing countries is prevalent despite limitations including higher capital costs, environmental pollution, and lower yields. This is primarily due to the very low solubility of barium sulfate in acidic solvents and HSE concerns associated with the latter. Here, with the aim of promoting the latter, important factors on the solubility of barite in oleum and sulfuric acid were investigated empirically. The dissolution process was then optimized using RSM and CCD, considering such independent parameters as temperature (140-180℃), acid concentration (70-90% v/v), initial barite particle size (50-200 mesh), and wt% barite dissolved as the dependent response parameter. The results indicated that optimized dissolution of 93.7% was obtained for oleum at 90% acid concentration, 140℃, 100-150 mesh barite particle size, while optimum solubility of 26.4% was achieved for sulfuric acid at 90% acid concentration, 180℃, 150-200 mesh barite particle size. Effective parameters on the barite solubility were found to be: acid concentration, solution temperature, and particle size, respectively.
- Introduction
Barium, an alkaline earth metal of group IIA in the periodic table, is found mostly in nature in the forms of barite (BaSO4) [1] or witherite (BaCO3) [2], often appearing as large tabular crystals, or divergent plates [3]. Barite solubility is low and has been the subject of many research interests in both geological and chemical processes since the late 18th century [4]. This has affected the industrial practice of Barium ion extraction for barium compounds production ever since, which has taken place customarily by reducing BaSO4 in reaction with coal in a process known as ‘black ash’ (in a rotary kiln at 800–1200°C) to form water-soluble BaS (as per reaction (1)), reacting further with suitable acids to produce useful barium salts [5, 6, 7]. Dissolution of barite, on the other hand, could offer a cheaper, cleaner, and more sustainable process with better yield, and in this work, we have tried to study and optimize it, with a view to employing this knowledge in designing a more environmentally sustainable process. But first, important aspects of the common black ash process development are reviewed here to highlight the practical aspects involved.
BaSO4(s) + 2C(s) → BaS(s) + 2CO(g) ΔH°rx = 208.388 kJ/m (1)
In Eq.1, the reduction reaction efficiency depends on the reactant’s ratio [8] and the carbon type used, offering various activation energy [7] and volatile matters [9]. Considering the intense ever-increasing environmental concerns, new improvements are being made to the black ash method in developed countries. However, a considerable proportion of barium salts produced globally originates in developing countries where weak monitoring and less motivation for progress, have made ‘black ash’ the prevalent production method. In practice, reactions 2 and 3 occur [7,10], indicating high energy consumption and polluting carbon dioxide emissions [11].
BaSO4(s) + 4CO(g) → BaS(s) + 4CO2(g) (2)
C(s) + CO2(g) → 2CO(g) (3)
The application of other agents such as natural gas, methane, and carbon monoxide has also been suggested to reduce barite in a fluidized bed [12]. However, this has offered few significant improvements in energy and pollution [13]. Even though the barite reduction with hydrogen (see Reaction 4) proposed by some workers [14] is said to circumvent the carbon dioxide emission fully, the method is not cost-effective in terms of energy.
BaSO4(s) + 4H2(g) → BaS(s) + 4H2O(g) (4)
In another study [11], sulfur was used as a barite-reducing agent according to reactions 5 and 6 to produce barium sulfide and sulfuric acid. This scheme seems to be capable of addressing the energy savings and emission discount, as the SO2 gas is turned into a useful common industrial acid and hence, the approach could be considered as a useful contender for replacing the black ash method.
BaSO4(s) + S2(g) → BaS(s) + 2SO2(g) (5)
S(s) + O2(g) → SO2(g) (6)
With around US$ 1.6bn market size, North America remains the largest global market in 2022 for barite [15]. India accounts for 35% of the global barite mine production followed by China at 25%, while Morocco, Kazakhstan, Mexico, USA, Turkey, Iran, and Russia, together account for around 40% in 2022 [16]. The global barite reserves in 2021 were estimated to be around 390 million tons of which Iran with more than a quarter of this, holds the greatest reserve [17]. More than 80% of barite mined globally is used as drilling mud in oil and gas wells, while the rest is used for barium compounds production such as BaSO4, BaS, BaCO3, BaCl2, Ba(NO3)2, BaTiO3, Ba(CH3COO)2, BaO, BaF2, Ba(ClO3)2, etc. in a variety of industrial and medical applications including pigment, filler, glass and lenses, advanced electronics and, X-ray examination[18].
Most research on barite solubility published in the literature is related to oil and gas industries where insolubility of barite presents substantial challenges. Many workers have focused on evaluating barite dissolution in different Aminopolycarboxylic acids as chelating agents including ethylene diamine tetra acetic acid (EDTA), diethylene triamine penta acetic acid (DTPA), and hydroxyethyl ethylene diamine tri acetic (HEDTA) acid, etc., where parameters such as pH, temperature, concentration, catalyst, chelating agents base, presence of oxalate ion, agitation effect, and dissolution time [19,20,21] are investigated. In a recent study, ‘macropa’, a macrocyclic descaling agent was proposed to remove barite, claiming to offer better solubility performance of around 11.4 g/l at pH of 8, as compared to 5 and 8 g/l, for EDTA and DTPA, respectively [22]. However, in general, there are reservations about relying upon such data primarily due to a lack of chemical understanding of the subject. Others have developed thermodynamic solubility models based on the Pitzer ion interaction theory to predict and control barite scale formation in different apparatuses [23-26] whereby barite solubility is estimated over wide ranges of temperature, pressure, and ionic compositions in geochemical and industrial processes in the presence of mixed electrolytes.
Furthermore, barite solubility has been investigated in sulfuric acid by several workers. Trenner and Taylor in 1931 studied the solubility relations for the BaSO4-H2SO4-H2O system at 25°C and the concentration range of 83-100 wt% acid. The solubility in absolute acid with a density of 1.853 g/cm3 was reported as 15.89 wt%. The system, however, demonstrated two solid phases at 25°C BaSO4 and probably BaSO4.H2SO4, with a transition at an acid concentration of about 85wt%. Using an accurate, and convenient conductance method, a distinct compound from the solid solution and adsorption was formed [27]. Interestingly the solubility decreased sharply to 0.05 wt% in a solution containing 83% concentrated acid [28]. Considering modern theories of strong electrolytes, this incredible decrease is somewhat irregular whilst realizing that the dielectric constant of absolute sulphuric acid is of the same order as water [27]. In another research, various combinations of acids and peroxide (H2SO4, HNO3, HF, H2O2) were employed in an attempt to determine the solubility of barite. However, these endeavors proved unsuccessful in yielding the desired information about barite’s solubility. This outcome arose primarily from the omission of a crucial step involving the dissolution of barite with the subsequent formation of barite as a precipitate. The only exception to this was the dissolution method employing sulfuric acid, which effectively and completely dissolved the barite sample while producing barite as a precipitate [29]. In their investigation of receiving barium sulfate from barite, Yermukhanova and Khatsrinov proposed the use of Oleum as a solvent for barite but did not offer additional details or information on this approach [2].
In this paper, the solubility of barite is investigated using oleum and sulfuric acid experimentally to measure barite’s maximum solubility. To produce barium salts, the initial step involves finding the optimal conditions for dissolving barite in a solvent capable of reacting salt metathesis. While previous research has shown a significant reduction in the solubility of barite in sulfuric acid as its concentration decreases, this study delved into various other factors impacts such as solution temperature, barite particle size, pressure, stirring speed (rpm), reaction time, and acid concentration on the barite solubility process. Then the solution temperature, barite particle size, and acid concentration were selected as operating parameters and the process was optimized using experimental design software. Moreover, in pursuit of achieving the highest possible barite solubility, both oleum and sulfuric acid were investigated as potential solvents for barite. It is worth noting that the nature of these two solvents bears a striking resemblance, albeit with a key distinction: oleum contains an elevated concentration of dissolved SO3 gas, enhancing its acidity and differentiating it from standard sulfuric acid.
- Materials and methods
2.1. Materials
The barite lumps used in this work were obtained from Madankavan Sialk in Kashan, with an average purity of about 95% based on XRD and XRF analyses (See sections 2-4 & 2-5). The oleum and sulfuric acid were acquired from Golbaran Acid Co., Ghazvin with 104.5% and 98% purity, respectively. Oleum concentration is represented in (100+X)% where X corresponds to the water mass (g) required to rescind all free SO3 available in a 100g oleum sample. XRD and XRF analysis was carried out using an X’Pert Pro (Panalytical Co., Netherland) and PW2404 (Philips, Netherland), respectively. For SEM tests a FEG SEM MIRA3 LMU (TESCAN, Czech Republic) equipped with EDX was employed. Size reduction of barite lumps was carried out using a laboratory jaw crusher DCFR 10*9 model, and a laboratory rod mill (Daneshfaravaran Co., Iran). Sieve analysis was carried out using a sieve shaker machine (Daneshfaravaran Co., Iran). General lab equipment was used for solubility and filtration purposes as per requirement and availability.
2.2. Experiment design
In order to reduce the number of experiments and material resources and also to save time in various processes, experimental design is a useful method for the control and optimization of the effective parameters in the process. Furthermore, it is useful for minimizing experimental errors and for the easy realization of the analyzed results. The statistical method of experimental design evaluated the effect of every parameter and their mutual interactions on the process. In the RSM method, an experimental design is designed to fit a model based on the least squares method. Then, the proposed model adequacy is evaluated using the analysis of variance (ANOVA). By this method, several experiments are designed, and the coefficient of the obtained mathematical model is estimated and the model’s applicability is finally analyzed [27,28] Table 1 shows the experimental conditions.
The effective parameters of solution temperature, acid concentration, and barite particle size are considered independent variables, and the weight percentage of barite dissolved is determined as the response variable (R). According to (Eq. 1) the weight percentage of barite can be measured, where C0 and Cm are the initial and final weights of barite in the process.
R= ((C0–Cm)/C0) 100 (1)
Twenty-two experiments including 3-level variables with six center points (Eq. 2) were designed and the experimental run order was randomized using the central composite design (CCD) method by Design Expert software (DX12)
N = 2k + 2k + nc (2)
where N is the number of experiments, k is the number of design factors, and nc is the number of center points. In the experimental design of this study for the dissolution of barite in oleum and sulfuric acid, in contrast to the temperature and concentration variables which are numeric, the barite particle size variable is in the class of categorical variables. Numeric variables can be any value in an interval, but categoric variables can only be certain values and This is due to the nature of the grading variable, which does not have a definite value and is considered as an interval between two values. Therefore, the number of tests varies from 20 to 22. The experimental design and the range of input variables are shown in Table 1. The experiments were performed according to Table 2.
Table 1. The input and output variables range.
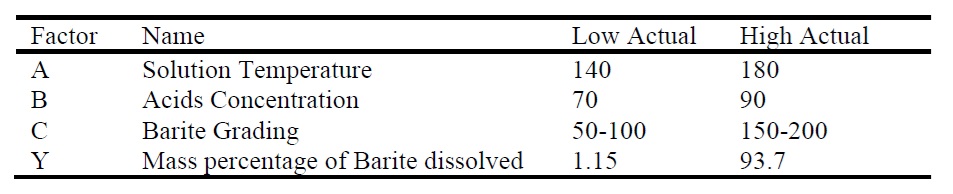
Table 2. Experimental design for the solubility of barite in oleum and sulfuric acid
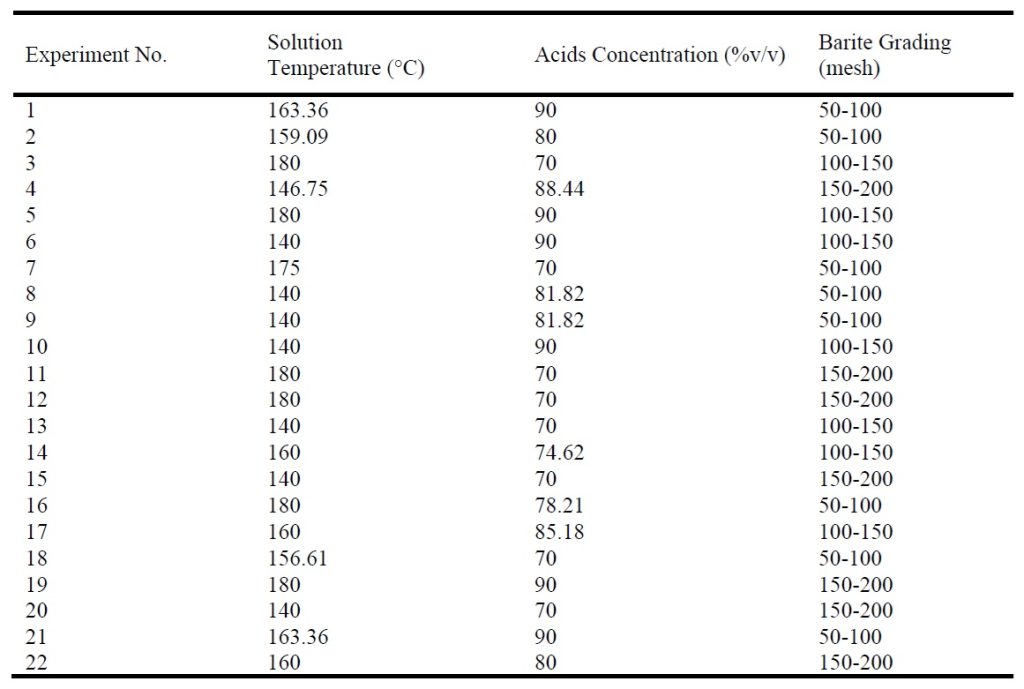
The correlation coefficient value (R2) of models was used to express the quality of polynomial models. The significance and adequacy of the models were evaluated using the Fisher variation ratio (F value) and probability value (Prob > F).
2.3. Solubility experiments
Minor surface impurities were washed using HCl (37%), before barite lumps were crushed, milled, and classified down to required powder sizes (50-200 mesh) using a laboratory jaw crusher and a 5L rod mill. The powder was washed again with the same HCl, and neutralized with de-ionized water, before being dried in an oven at 60℃ for 24 hours. Three different mesh sizes of (50-100), (100-150), and (150-200) were examined. Oleum and sulfuric acid solutions were prepared in 100ml samples of 70%, 80%, and 90% v/v. 20g of barite was added to the 100ml sample solution at various temperatures of 140°C, 160°C and 180°C, and stirred magnetically for 30 min (determined empirically) as per Figure 1, where the experiments were carried out in a safe hooded environment under stringent precautions deemed necessary for such hazardous conditions. Important parameters investigated in this work include initial barite grade, acid concentration, and temperature.
Despite its low solubility, the following reactions could be considered where barite splits into its constituent ions namely free Ba2+ and SO42- ions in solution:
H2O7S2 + H2O → 2H2SO4 (7)
H2SO4 + H2O(l) → H+(aq) + HSO4–(aq) (8)
HSO4– + H2O(l) ⇋ H+(aq) + SO42-(aq) (9)
BaSO4 → Ba2+ + SO42- (10)
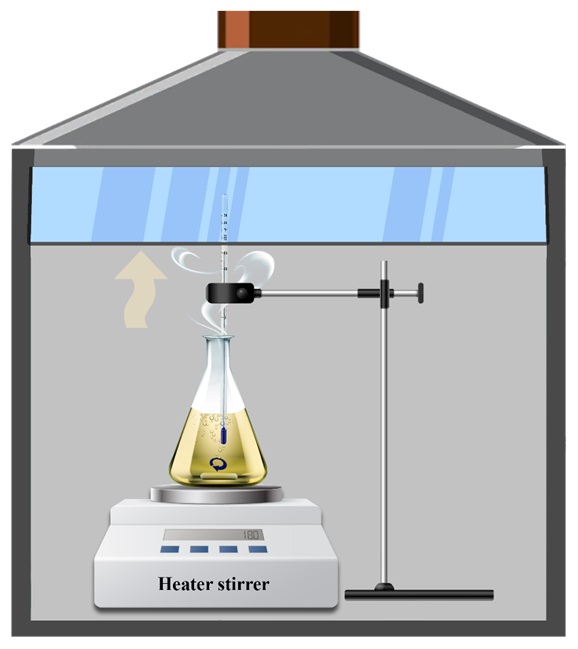
Figure 1. Solubility setup used for barite dissolution in oleum
Owing to the limitations imposed by highly acidic and operational temperature, the undissolved barite is filtered out and weighed, using a G3 sintered glass funnel using a simple setup as per Fig.2.
After the filtration process, the undissolved barite remains on the funnel, which is washed with distilled water and checked with pH paper to ensure that it is neutral and free of acid. Then the undissolved barite and funnel are placed in an oven at a temperature of 150°C for 30 minutes to dry completely. By measuring the dry funnel weight before and after the filtration operation, the amount of undissolved barite is obtained.
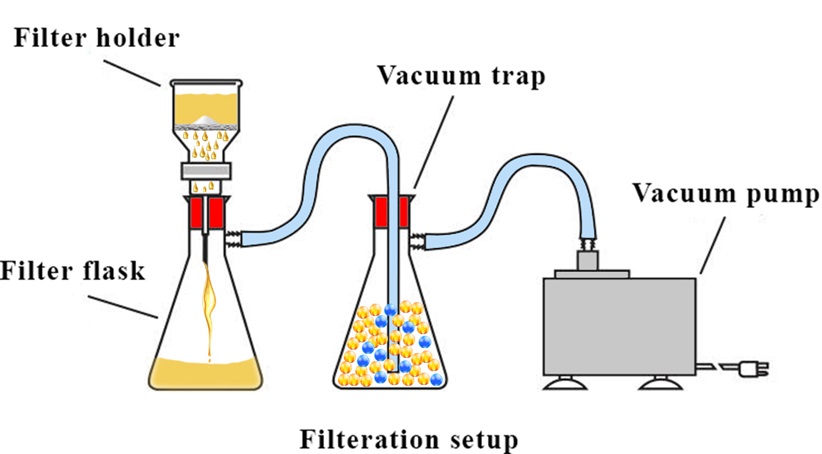
Figure 2. Filtration setup for separating and weight measuring of undissolved barite
2.4. X-ray powder diffraction
Minerals found in nature and many materials produced in various industries and research laboratories have a crystalline structure that consists of a series of atomic plates in a specific order. If a beam (preferably X-ray) hits these plates, diffraction occurs according to Bragg’s formula (2dsinθ = nλ) at a certain angle. According to the graph below, there is a good overlap and coordination between the barite peak list and XRD analysis.
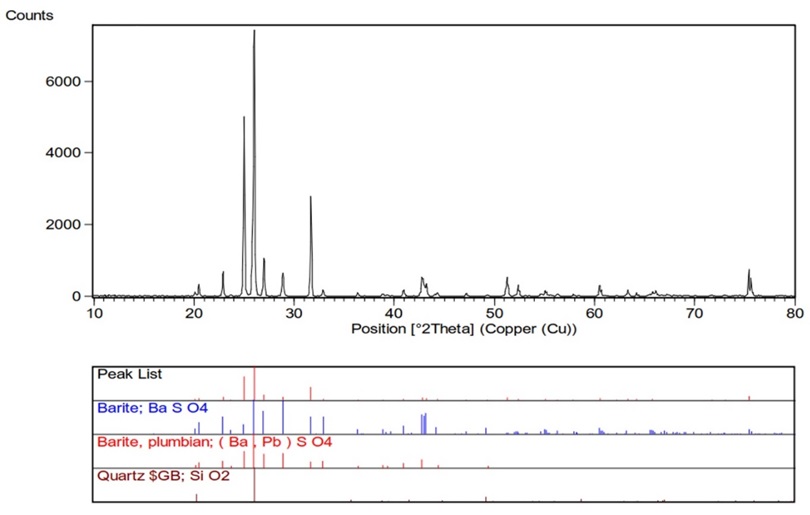
Figure 3. XRD analysis of barite powder
2.5. X-ray fluorescence
XRF analysis was used to determine the percentage of the elements in the barite sample. Table 3 shows the barite components. As can be seen from the result of the analysis, the main impurity belongs to strontium (Sr) with 3.212% which is in the same group of alkaline earth metals as barium in the periodic table, and in case of properties, they are highly similar to each other and would not make problem in our solubility study. As the sulfate compounds exist in the barite strontium this. The strontium in this context appears in the form of strontium sulfate.
Table 3. of prepared barite for testing

2.6. Scanning electron microscopy and EDX
Scanning electron microscopy (SEM) was used for barite characterization. The samples were prepared with a coating of a thin gold layer and then studied using SEM.
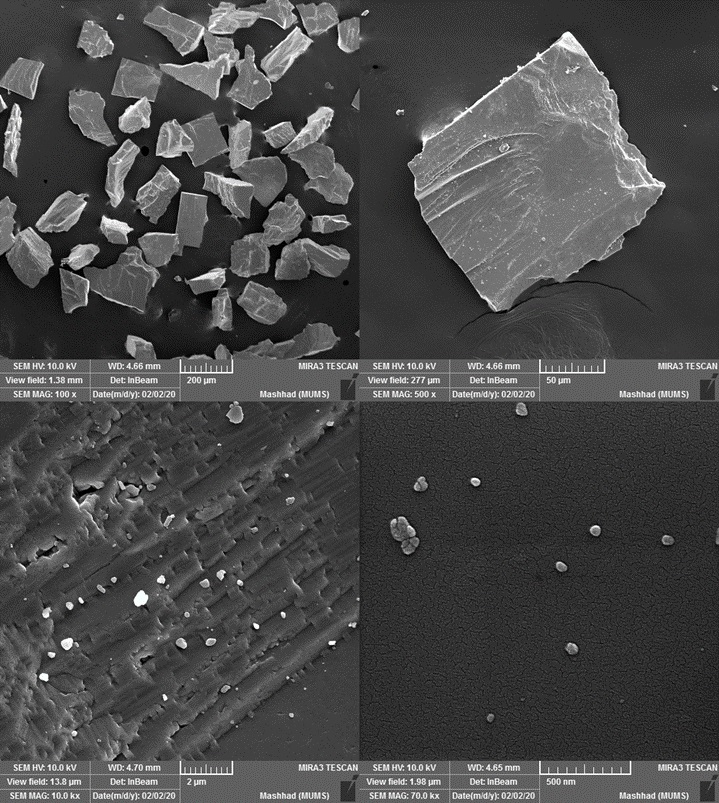
Figure 4. Barite powder SEM analysis
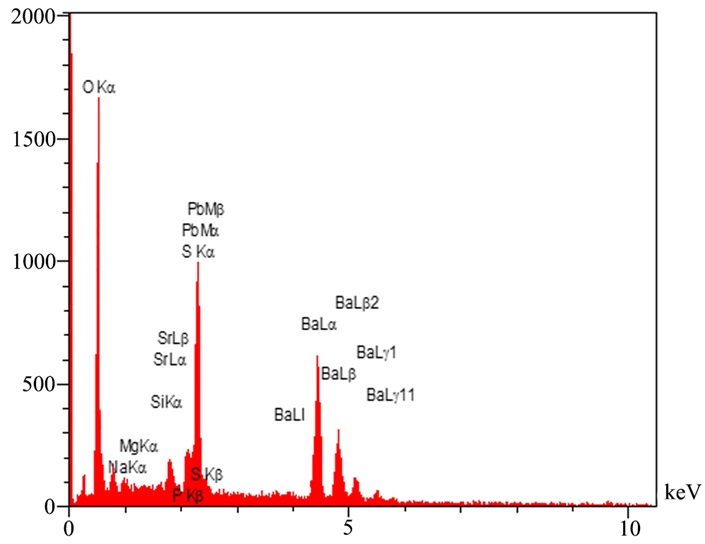
Figure 5. Barite powder EDX analysis
- Results and discussion
3.1. Model performance evaluation
Analysis of variance (ANOVA)
Table 4 shows the variance analyses of regression variables of the dissolving barite in oleum and sulfuric acid models, respectively. The F value and p-value of the dissolving barite in the oleum model were 701.61 and < 0.0001, and it was 221.00 and <0.0001 for the dissolving barite in the sulfuric acid model which indicated that the models were significant. The Prob > F values of model terms of less than 0.05 indicate that they are significant [32]. B, AB, AC, BC, B2, and A2B are significant factors and A, C, and A2 are insignificant factors in the dissolving barite in the oleum model (A: Solution Temperature, B: Acids Concentration and C: Barite Grading). A, B, C, AB, AC, A2, and A2B are significant factors and BC, B2, and A2C are insignificant factors in the dissolving barite in the sulfuric acid model.
Table 4. ANOVA analysis results of the developed model for dissolving barite in (a) oleum and (b) sulfuric acid
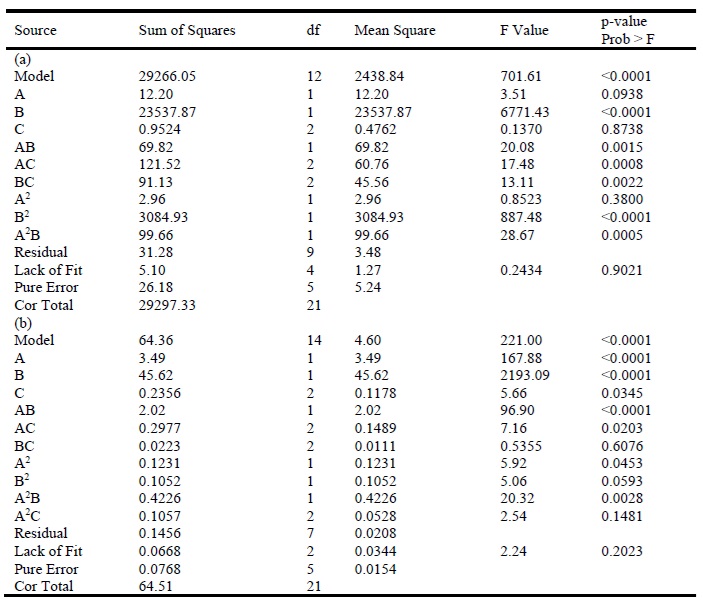
The statistical measures and model performance of dissolving barite in oleum and sulfuric acid are presented in Table 5. The model’s adequate precision ratio is an adequate signal for the appropriate model which was 64.4789 for the dissolving barite in oleum model and 46.9599 for the dissolving barite in sulfuric acid model (adequate precision > 4). The correlation coefficient value (R2) for an appropriate model should be at least 0.8 and its high value shows that the calculated results using the model and the observer results are close to each other [30]. The R2 values for dissolving barite in oleum and sulfuric acid are 0.9989 and 0.9977, respectively, which indicates that the models are appropriate. The results show that the models for predicting dissolving barite in oleum and sulfuric acid were considered reasonable. The regression models for dissolving barite in oleum and sulfuric acid, in terms of their coded factors, are expressed by Eq. (7) and (8), respectively.
Solubility in oleum =
11.47 – 0.5020A + 33.84B + 0.6302C[1] + 0.4419C[2] – 3.78AB – 3.73AC[1] + 1.5AC[2] – 4.77BC[1] + 2.23BC[2] + 0.7927A2 + 32.69B2 + 12.68A2B
(7)
Solubility in sulfuric acid=
1.23 + 0.4143A + 1.4B -0.959C[1] – 0.0320C[2] – 0.5752AB – 0.0118AC[1] – 0.1111AC[2] – 0.0720BC[1] + 0.0366BC[2] – 0.2207A2 + 0.3250B2 + 0.8354B2 – 0.0687A2C[1] + 13.47A2C[2]
(8)
The diagnostic plots such as studentized residual normal probability plots are used to judge the adequacy of the models. If the points follow a straight line in a normal probability, it shows that the residuals follow a normal distribution [30,31]. The studentized residual normal probability plots of dissolving barite in oleum and sulfuric acid are shown in Fig. 3. It shows that the data have a normal distribution.
Table 5. Statistical measures and models performance of dissolving barite in oleum and sulfuric acid

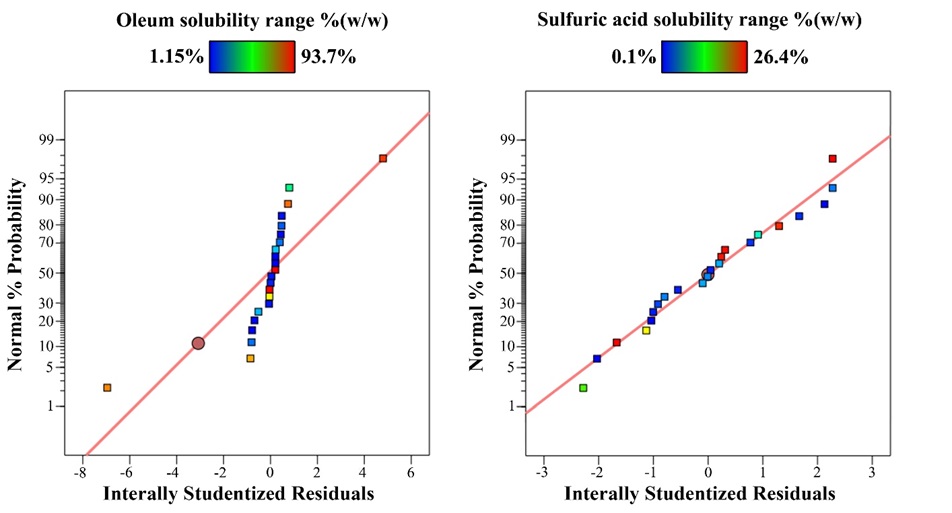
Figure 6. Studentized residual normal probability plots for barite solubility in oleum and sulfuric acid
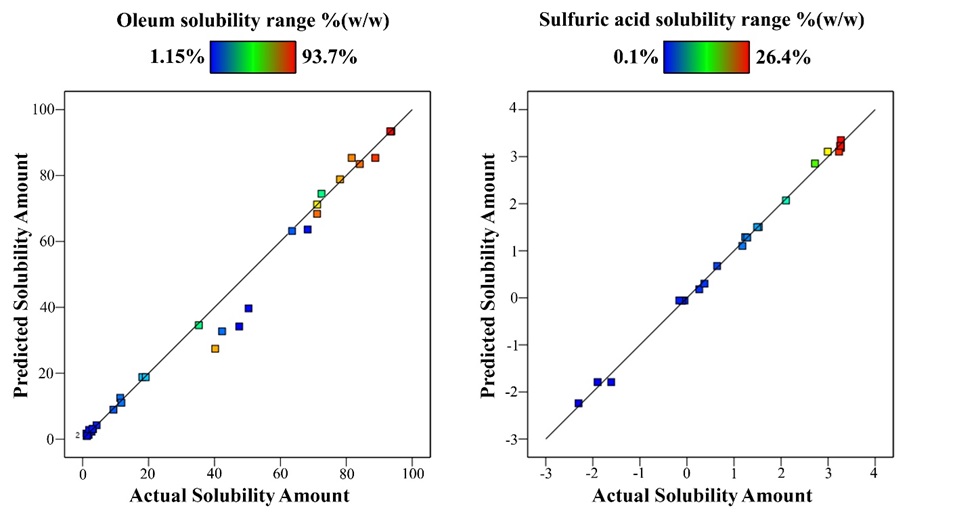
Figure 7. Actual and predicted barite solubility amount comparison in oleum and sulfuric acid
In the following, we will analyze the results of barite dissolution experiments in oleum and sulfuric acid, validate the model defined for this process, investigate the effect of different variables on the process, and optimize the obtained responses.
One of the statistical methods that significantly helps to review and analyze the test results is the use of data from the analysis of the variance table. Analysis of variance, which represents the distribution of the scatter of all data between the constituent factors, is based on the Fisher test.
In this step, the sum and average of the squares, the degree of freedom, the F and P statistics of each of the selected parameters, and the remainder are calculated. These values are presented in Tables 4-5 and 4-6.
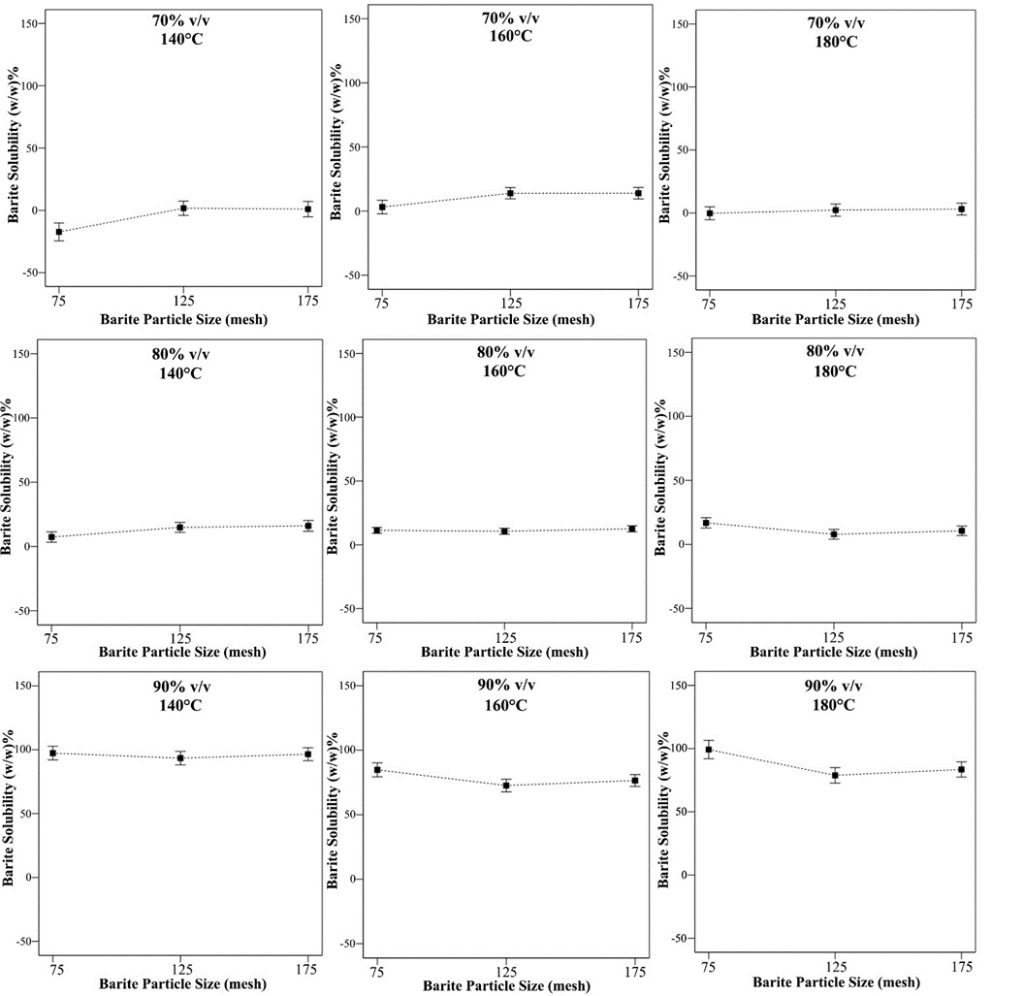
Figure 8. Barite particle size effect on solubility at different concentration and temperature conditions
Response surface methodology
With increasing temperature at 70% oleum concentration in different gradings, the process is similar and the maximum dissolution in each grading occurs in the temperature range of 160°C to 170°C. At 80% oleum concentration, with increasing temperature for 100-150 mesh and 150-200 mesh gradings with decreasing barite dissolution, but at 50-100 mesh grading, increasing temperature leads to increasing solubility. Also, at 90% oleum concentration, the trend of the graphs is almost the same, with the highest solubility for 50-100 mesh grading at 180°C and the highest solubility for 100-150 mesh and 150-200 mesh gradings at 140°C.
Increasing the temperature at concentrations of 70% and 80% sulfuric acid in different gradings did not have a significant effect on dissolution. But at a concentration of 90% with increasing temperature in all three gradings, ln(Barite Dissolution) first decreases and then increases.
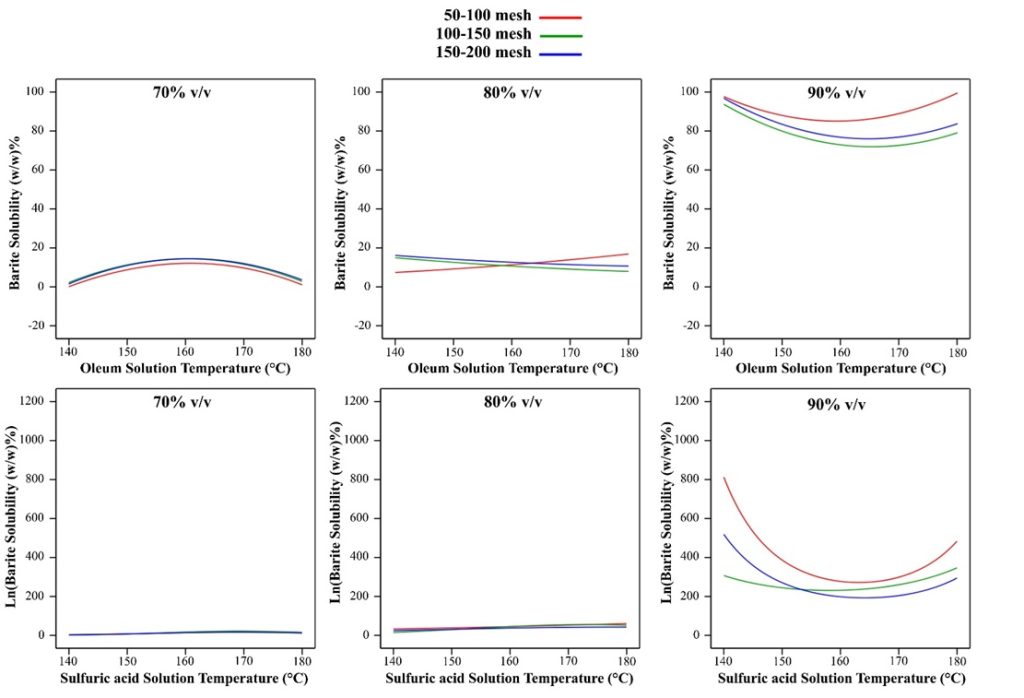
Figure 9. Oleum and sulfuric acid solutions temperature alteration effect on barite solubility in constant barite particle size and acid concentration
Oleum concentration and barite solubility are directly related. Variations in barite solubility in 100-150 mesh and 150-200 mesh gradings are very similar to each other, and for 50-100 mesh grading, the solubility of barite in all concentrations increases with increasing temperature.
Concentration change at 140°C has the greatest effect on dissolution compared to other temperatures, and 100-150mesh grading has the greatest increase in dissolution with increasing concentration at all temperatures. At 140°C, 150-200 mesh grading has more solubility than 100-150mesh grading, but at 160°C and 180°C, 100-150 mesh grading has more solubility than 150-200mesh grading.
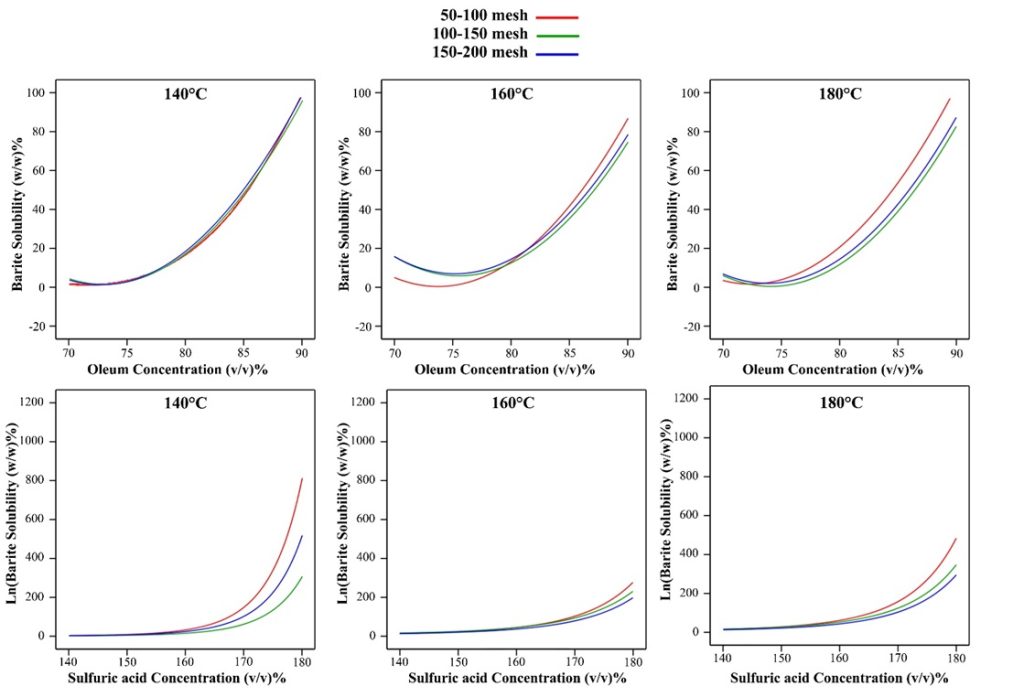
Figure 10. Oleum and sulfuric acid concentrations alteration effect on barite solubility in constant barite particle size and solution temperature
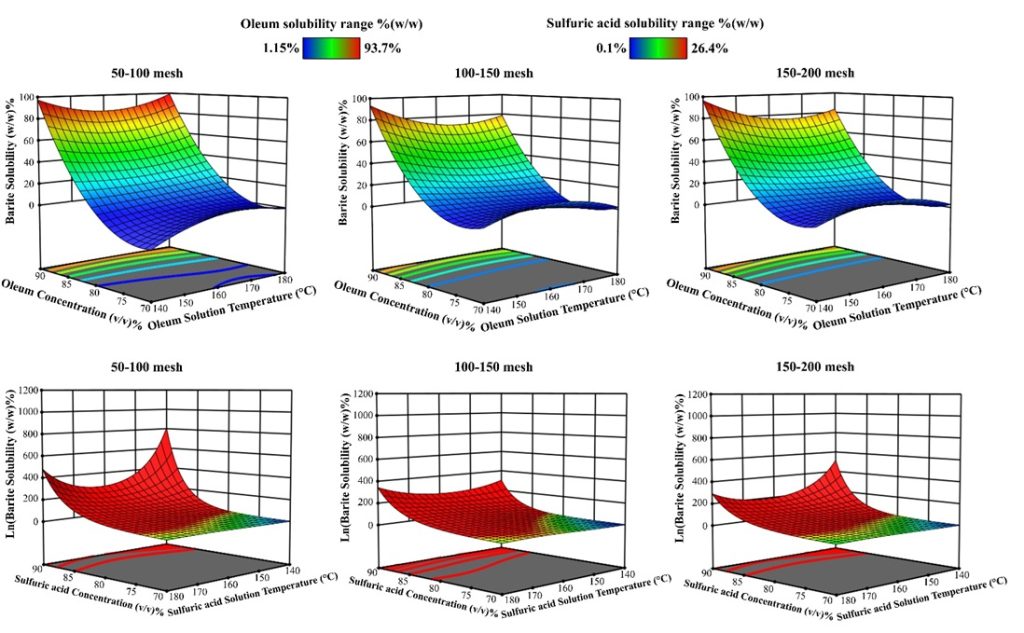
Figure 11. 3d schematic of Oleum and sulfuric acid concentrations alteration and solutions temperature change effects on barite solubility in constant barite particle size
References
[1]. W. M. Haynes, ed., CRC Handbook of Chemistry and Physics, CRC Press/Taylor and Francis, Boca Raton, FL, 95th Edition.
[2]. Tasbolatovna YS, Ilyich KA. The most important technologies of receiving barium sulfate from barite. European science. 2020(6 (55)):30-4.
[3]. Britannica, The Editors of Encyclopaedia. “barite”. Encyclopedia Britannica, 25 Jan. 2018, https://www.britannica.com/science/barite. Accessed 21 November 2021.
[4]. Melcher AC. The Solubility of silver chloride, barium sulphate, and calcium sulphate at high temperatures. Journal of the American Chemical Society. 1910 Jan;32(1):50-66.
[5]. C.W. Blount, Barite solubilities and thermodynamic quantities up to 300 degrees C and 1400 bars, American Mineralogist, 62 (1977) 942-957
[6]. Lung, C.; Chen, S.; Wu, J. Study on the reducing conditions of the barite in Boyang. J. Nanchang Univ. 1991, 15 (1), 1-6
[7]. Bafghi, M. S.; Yarahmadi, A.; Ahmadi, A.; Mehrjoo, H. Effect of the type of carbon material on the reduction kinetics of barium sulfate. Iran. J. Mater. Sci. Eng. 2011, 8, (3)
[8]. Study of thermal reduction of barium sulphate for barium sulphide preparation Proc. Int. Conf. Environ. Eng. (2017)
[9]. Effect of nature of coal on carbothermal reduction of barites Orient. J. Chem. (2014)
[10]. Jagtap, S. B.; Pande, A. R.; Gokarn, A. N. Effect of catalysts on the kinetics of reduction of Barite by carbon. Ind. Eng. Chem. Res. 1990, 29 (5), 795-799.
[11]. Wei Zhang, Yong Zhou, Jiahua Zhu, and Yanlin Pan, New Clean Process for Barium Sulfide Preparation by Barite Reduction with Elemental Sulfur, Industrial & Engineering Chemistry Research 2014 53 (14), 5646-5651
[12]. Shakhtakhtinskii, G.; Yusubov, R.; Samedova, A. Reduction of a granulated Barite concentrate by converted natural gas in a fluidized bed. Azerb. Khim. Zh. 1972, 4, 114-116.
[13]. Jamshidi, E.; Ebrahim, H. A new clean process for barium carbonate preparation by Barite reduction with methane. Chem. Eng. Process.: Process Intensif. 2008, 47 (9), 1567-1577
[14]. Sohn, H. Y.; Savic, M.; Padilla, R.; Han, G. A novel reaction system involving BaS and for converting to elemental sulfur without generatingnpollutants: Part I. Feasibility and kinetics of reduction with BaS. Chem. Eng. Sci. 2006, 61 (15), 5082-5087.
[15]. Barite market, https://www.futuremarketinsights.com/reports/global-barite-market
[16]. World barite mine production from 2010 to 2022, by country https://www.statista.com/statistics/273330/baryte-production-output-worldwide/
[17]. Gu H, Yang Y, Guo T, Xiao J, Gao Y, Wang N. Review on treatment and utilization of barium slag in China. Journal of Environmental Management. 2023 Jan 1;325:116461.
[18]. Hanusa, Timothy P.. “barium”. Encyclopedia Britannica, 26 Oct. 2020, https://www.britannica.com/science/barium.
[19]. BAGERI BS, Mahmoud MA, Shawabkeh RA, Abdulraheem A. Evaluation of Barium Sulfate (Barite) Solubility Using Different Chelating Agents at a High Temperature. Journal of Petroleum Science and Technology. 2017 Feb 20;7(1):42-56.
[20]. GEIZILA A.P. ABIBGEORGIANA F. DA CRUZALEXANDRE S.L. VAZ JUNIOR. Study of barium sulfate dissolution by scale dissolver based on solutions of DTPA. Engineering Sciences. An. Acad. Bras. Ciênc. 90 (3). Jul-Sep 2018
[21]. Sazali RA, Kechik NA, Yahya E, Mat-Shayuti MS. Study of Barium Sulfate Scale Dissolution into Ethylenediaminetetraacetic acid (EDTA). InIOP Conference Series: Materials Science and Engineering 2020 Apr 1 (Vol. 778, No. 1, p. 012112). IOP Publishing.
[22]. Hassan A, Kamounah FS, Pittelkow M, Solling T, Mahmoud M. Barite Removal Using Macropa: Simulation and Solubility Investigations. Energy & Fuels. 2022 Aug 3;36(16):9101-10.
[23]. Hossein Safari, Amin Shokrollahi, Mohammad Jamialahmadi, Mohammad Hossein Ghazanfari, Alireza Bahadori, Sohrab Zendehboudi, Prediction of the aqueous solubility of BaSO4 using pitzer ion interaction model and LSSVM algorithm, Fluid Phase Equilibria, Volume 374, 2014, Pages 48-62
[24]. Zhaoyi D, Amy K, Fangfu Z. A Thermodynamic Model for the Solubility Prediction of Barite, Calcite, Gypsum, and Anhydrite, and the Association Constant Estimation of CaSO4 (0) Ion Pair up to 250 C and 22000 psi. Journal of Chemical & Engineering Data. 2014;60(3):766-74.
[25]. Dai Z, Kan AT, Shi W, Yan F, Zhang F, Bhandari N, Ruan G, Zhang Z, Liu Y, Alsaiari HA, Lu YT. Calcite and barite solubility measurements in mixed electrolyte solutions and development of a comprehensive model for water-mineral-gas equilibrium of the Na-K-Mg-Ca-Ba-Sr-Cl-SO4-CO3-HCO3-CO2 (aq)-H2O system up to 250 C and 1500 bar. Industrial & Engineering Chemistry Research. 2017 Jun 14;56(23):6548-61.
[26]. Blount CW. Barite solubilities and thermodynamic quantities up to 300 degrees C and 1400 bars. American Mineralogist. 1977 Oct 1;62(9-10):942-57.
[27]. N. R. Trenner and H. A. Taylor. The Journal of Physical Chemistry 1931 35 (5), 1336-1344
[28]. Arbaoui Mohamed Ali, Hacini Messaoud, Barium Sulphate Deposits, Energy Procedia, Volume 157, 2019, Pages 879-891.
[29]. Fouad S. Al-Kaabi, Raghad A. Hussein, Mustafa A. Abdulkareem, Dissolution of barite using coordination chemistry: Optimization and characterization, Results in Chemistry, Volume 5, 2023, 100791.
[30]. Bashir MJ, Aziz HA, Yusoff MS, Adlan MN (2010) Application of response surface methodology (RSM) for optimization of ammoniacal nitrogen removal from semi‑aerobic landfill leachate using ion exchange resin. Desalination 254:154–161
[31]. Roosta, M., Ghaedi, M., Daneshfar, A., Darafarin, S., Sahraei, R., Purkait, M., 2014. Simultaneous ultrasound-assisted removal of sunset yellow and erythrosine by ZnS: Ni nanoparticles loaded on activated carbon: optimization by central composite design. Ultrason. Sonochem. 21, 1441e1450
[32]. Ahmadi M, Vahabzadeh F, Bonakdarpour B, Mofarrah E, Mehranian M (2005) Application of the central composite design and response surface methodology to the advanced treatment of olive oil processing wastewater using Fenton’s peroxidation. J Hazard Mater 123:187–195
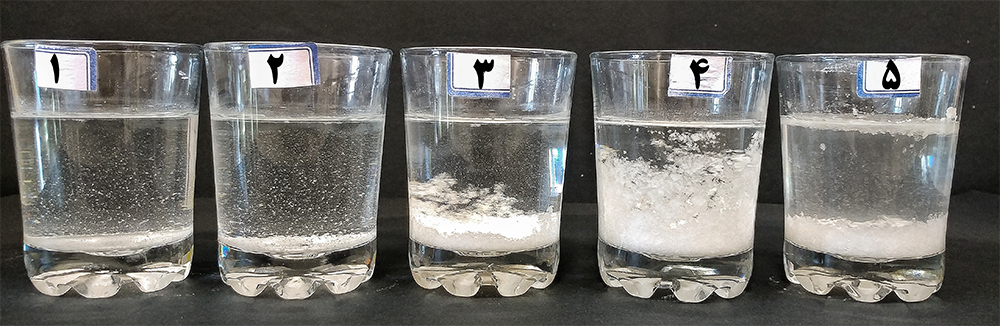
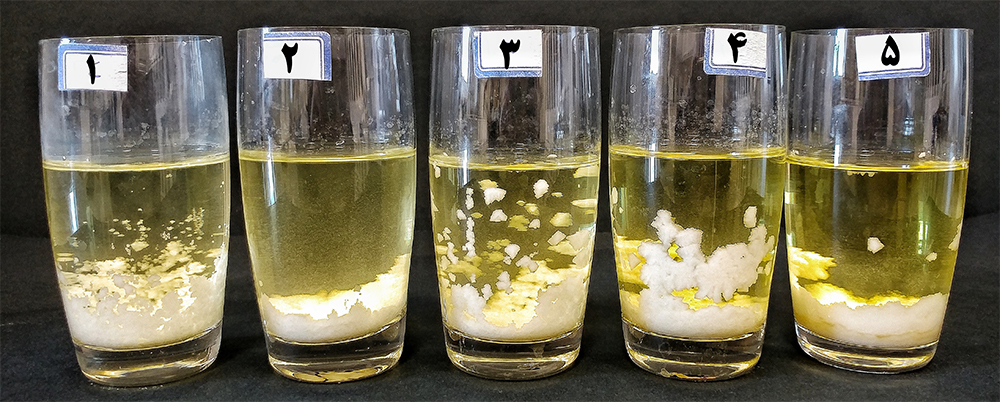
Crystallization optimization of barium nitrate and barium chloride salts in different densities for maximum crystallinity
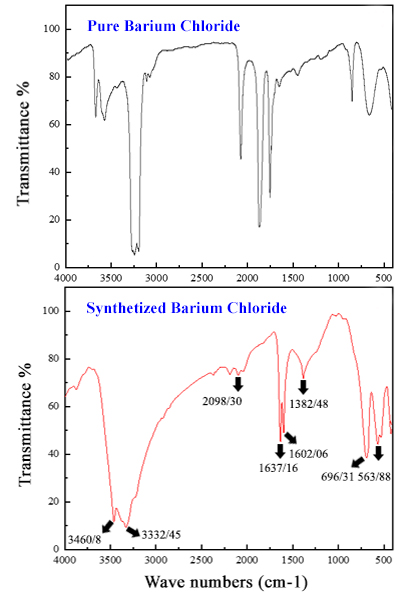
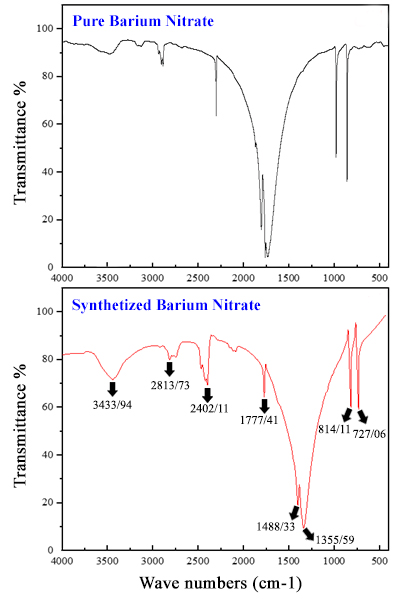